How Supply Chain Sustainability Benefits From Improved Materials Management
This is a guest post by Matilda Odell.

Businesses that import or export goods cannot afford to turn a blind eye to the detrimental impact their supply chain processes have on the communities around them. From air and noise pollution to soil degradation and resource depletion, the impact can be far-reaching and long-lasting.
However, supply chain sustainability presents an opportunity to not only make a profit but also do environmental good.
Effective materials management is a crucial aspect of supply chain management for manufacturers. It involves planning and executing your supply chain to meet your raw materials requirements, including material flow, availability, quality, price, and demand. This encompasses all stages from the purchase of raw materials to storage, loading and unloading in a warehouse, transporting, and receiving.
In the following sections, we will delve into the sustainability benefits of efficient materials management and explore ways to enhance your own business’ materials management process.
1. Reduce Raw Material and Inventory Waste
Acquiring more raw materials than necessary increases the likelihood of waste, eating into profits and contributing to landfills. In addition, purchasing substandard, defective, or unnecessary raw materials wastes resources and exacerbates environmental impact.
Overproduction can also result from excess storage of raw materials, tempting businesses to convert them into end-products in the hopes of eventually matching demand. However, this can lead to excess inventory, obsolete or expired goods, and inventory waste. Shockingly, around 8% of excess inventory, equivalent to about $163 billion globally, becomes waste each year.
Efficient materials management aims to acquire the precise type, quantity, and quality of raw materials required, avoiding waste and minimizing the possibility of overproduction.
2. Decrease Pollution
Transporting materials to production facilities using air, road, rail, or sea transport contributes to environmental damage through increased pollution from fuel combustion and noise pollution. In fact, according to the WTO’s 2021 Trade and Climate Change brief, international import-export trade (including the production and transport of goods) is responsible for generating 20-30% of global greenhouse gas emissions.
Similarly, operating production machinery for extended periods generates additional air and noise pollution.
Efficient materials management reduces unnecessary transport and production machinery use, limiting carbon and noise footprint. By moving and manufacturing only what you need, businesses can reduce the frequency of equipment operation, leading to a smaller environmental impact.
3. Reuse Materials
The concept of reusing and recycling is familiar in households, where bottles, boxes, and containers are often repurposed for different uses. Similarly, industrial and commercial waste often contains items that are not entirely useless.
Yet, businesses regularly dispose of large quantities of waste that could be repurposed or reused internally. In the US alone, industrial waste production reaches a staggering 7.6 billion tons annually.
Good materials management involves identifying opportunities to repurpose raw materials and end-products that would otherwise become waste. This approach reduces waste and creates additional value for businesses.
4 Tips to Easily Improve Your Materials Management
1. Develop a Materials Management Plan
The foundation of efficient materials management is a solid materials management plan. This plan should outline a business’s strategies, goals, and intended outcomes for materials management while addressing any current process weaknesses.
Let’s say that a company with excess inventory and high storage costs develops a materials management plan with these goals:
- reducing excess inventory
- optimizing raw material purchasing
- implementing just-in-time inventory management.
All relevant stakeholders, including production teams, finance teams, logistics providers, and suppliers, are involved in the plan’s development. By collaborating to identify weaknesses in the current process and develop strategies for improvement, the company can create a more efficient materials management process that reduces waste, lowers costs, and adds value to the business.
2. Implement Inventory Management Practices
Inventory management is arguably the most important pillar of materials management. Without proper inventory control, businesses risk overstocking or understocking raw materials, which can lead to waste, increased costs, and missed production deadlines.
Utilizing inventory software, barcode technologies, and material tracking tools can help ensure that raw materials are available when needed and prevent overstocking.
For example, a manufacturing company implements a just-in-time inventory system. Then, the company can use real-time data to make informed purchasing decisions and ensure that raw materials arrive only when they’re needed for production.
3. Build Strong Supplier Relationships
Suppliers are at the center of materials management. If they are not fulfilling their end of the bargain, the high efficiency of your internal materials management process won’t matter much.
Choose suppliers with a track record for reliability and scalability. Building strong relationships with such suppliers can help ensure that materials are delivered on time, meet specifications, and are of the right quality and price.
For instance, a company that imports goods from overseas could face significant delays and disruptions if its suppliers are unreliable or do not follow international regulations. This could result in lost sales opportunities, unhappy customers, and increased costs.
4. Continuous Monitoring, Analysis, and Improvement
That your materials management process worked well in the past does not mean it will work as well today and in the future. How do you know how well your process is working? Data analysis. Continuously collect and analyze data on supplier performance, material use, and inventory levels to pick up demand/supply trends and market shifts then make the appropriate decisions.
Where possible, leverage artificial intelligence, machine learning, the Internet of Things, and other emerging technology to improve the process. Regularly review supply chain metrics and make changes to the process in order to increase efficiency, minimize waste, and boost customer satisfaction.
For example, a business that exports perishable foods could use IoT sensors to track the temperature of the food during transit, and analyze the data to ensure they arrive at their destination in optimal condition.
Conclusion
Improved materials management is a key aspect of achieving sustainability in the supply chain. By optimizing the use of resources and reducing waste, businesses can not only achieve cost savings and competitive advantage but also contribute to a cleaner environment. Good materials management can help improve the eco-sustainability of sourcing and minimize negative environmental impact.
There are at least dozens of possible strategies for environmental sustainability and not all will work for you. Evaluate your supply chain, determine the most suitable strategy, apply it, and continuously improve.
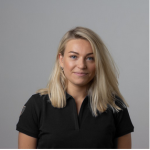
This was a guest post by Matilda Odell.
Author Bio
Matilda Odell works as the Content Creation Specialist at TAWI, a brand by Piab Group, which enables smart lifting optimized for people and businesses. Piab helps its customers to grow by transforming their businesses with increased automation. If you have any questions about lifting equipment such as lifting trolleys or other lifting devices, Matilda is the person to talk to.